The element zirconium is found in igneous rock such as granite and occurs as the naturally occurring oxide, baddeleyite (ZrO2) and more commonly as a compound with silica: zircon (ZrSiO4).
The weathering of igneous rock has led to the formation of large secondary deposits in beach sands. These deposits are generally associated with other heavy minerals sand such as imenite and rutile. Zircon is often mined as a by-product of these minerals.
Australia and South Africa have the largest commercial deposits of zircon while there are also significant deposits in the USA and India.
While a considerable amount of zircon sand is used in the production of refractories, glass and glazes it is finding increased application as feedstock for the production of added value chemicals and high purity oxides.
Over the last 10 years China has been playing an increasingly important role in the production and refining of these zirconium chemicals and oxides and now accounts for more than 60% of the world's output.
The caustic decomposition of zircon sand is a common process route for the production of a high purity zirconium oxychloride. This compound is used as a raw material for applications such as the production of titanium pigments and also as a pre-cursor for the production of a range of zirconium chemicals such as zirconium carbonate and zirconium hydroxide.
Thse basic chemicals are used in a wide range of applications including antiperspirants, paint driers, leather tanning, inks and catalysis. They are also used as the raw materials for the production of high purity chemically precipitated zirconium oxides.
ABSCO Materials supplies a range of high purity zirconium chemicals.
There are 2 main types of monoclinic zirconium oxide: one is from a thermal route and the direct fusion of zircon sand; and the other is the chemical precipitation of zirconium chemicals.
Monoclinic Zirconium Oxide, fused
The dissociation of zirconium oxide and silica can be carried out at high temperatures in an electric arc furnace to produce a fused zirconium oxide. The silica is reduced to the volatile silcon monoxide that reoxidises at the furnace mouth and is recovered in dust collectors as silica fume. The zirconia is reduced to the carbide and can be roasted in air to produce the fused zirconium oxide.
Fused zirconium oxide is a lower purity oxide, typically in the range of 98-99% ZrO and is used in refractories, pigments and abrasives. With the reduced availability of baddeleyite, fused zirconium oxide has become the substitute.
For many applications of fused zirconia the particle size distribution is very important. ABSCO Materials supplies a range of mesh sizes and finer particle powders and can supply powders tailored to individual specifications.
Monoclinic Zirconium Oxide, chemically precipitated
Chemical preparation, calcination and milling stages lead to the production of high purity chemical zirconias with specific and very individual physical characteristics. Process control enables very specific particle morphology, particle size and surface area which all greatly efffect the powders' performance.
ABSCO Materials supplies a range of chemcal zirconia powders with different purities, from 99.0 to 99.99% ZrO2, and also physical characteristics including particle size and surface area. ABSCO can also work with customers in the production of tailored powders to meet individual requirements.
ABSCO Materials supplies specialist zirconium oxide powders for use in structural ceramics, electro ceramics, thermal barrier coatings and refractories.
Monoclinic zirconium oxide can be restricted in its applications due to the phase transformations it undergoes during heating. These phase transformations lead to changes in volume resulting in structural cracking and failure. These phase alterations can be controlled by the addition of dopants known as stabilisers. Once stabilised, zirconia can be used in applications running at temperatures in excess of 2200 degrees centigrade.
ABSCO Materials offers a range of stabilised fused and co-precipitated zirconia powders.
Stabilised Zirconium Oxide, fused
Fused zirconium oxide can be stabilised during the fusion process by the addition of stabilisers such as yttria, magnesia and calcia. After fusion the material is crushed and milled to different particle sizes. ABSCO Materials supplies a range of YSZ, MgSZ and CaSZ powders with particle size distributions produced for specific applications or to customer specification.
Stabilised Zirconium Oxide, chemically co-precipitated
The chemical co-precipitation of intermediate zirconium and dopant compounds produces a very homegenous product with the doping element well dispersed within the structure. The precipitate is then calcined under controlled conditions to produce very specific particle size, morphology and surface area. All of these physical characteristics are very important in the powder's performance.
ABSCO Materials offers a range of yttria and magnesia stabilised co-precipitated zirconia powders for structural/engineering ceramics and refractories.
Stabilised zirconia powders can be supplied as raw powders or in granular form for spray coating or pressing.
Pure zirconium oxide (unstabilised) is monoclinic at room temperature but its structure changes to a tetragonal form at around 1000 degrees C. With this phase change there is a large volume change that results in structural cracks leading to a very low thermal shock resistence.
Partial stabilisation of zirconia occurs with the addition of a dopant material such as 3-4mol% yttria, 2-3mol% magnesia or 8mol% calcia. This leads to a mixture of structural phases at different temperatures. A mixture of cubic, monoclinic and some tetragonal phase up to 1000 degrees C. and tetragonal at higher than 1000 degrees. Due to the tetragonal phase at higher temperatures partially stabilised zirconia is also known as tetragonal zirconia polycrystal (TZP). It is generally believed that microcracks and induced stress amongst the different phases are reasons for the toughening in partially stabilised zirconia.
Partially stabilised zirconia tends to be used when high temperatures are needed. The low thermal conductivity ensures a low heat loss and the high melting point (2,700 degrees C.) means stabilised zirconia regreactories can be used in temperatures in excess of 2200 degrees C. Partially stabilised zirconia is also finding increased application in specialist structural/engineering ceramics.
Fully stabilised zirconia is generally achieved with dopant levels of 8mol% yttria, 16mol% magnesia or 16mol% calcia. A fully stabilised zirconia has a structure which is a cubic solid solution which has no phase transformation from room temperature up to 2500 degrees C. Fully stabilised zirconia is a very good ion conducting ceramic and is used in applications such as oxygen sensors and solid oxide fuel cells.
The main applications for zircon sand are in ceramics, refractories, TV glass and the production of zirconium oxides (zirconias) and zirconium chemicals. The production of glaze emulsions in the ceramics industry was the greatest consumer in 2008 at around 600,000mts. Refractories use both zircon sand and zirconia and consumed in the region of 200,000 mts. The foundry industry used in the region of 150,000mts in 2008 with the USA, Europe and now China being the biggest users. Around 90,000mts of zircon was used in the production of TV glass with Asia now accounting for 90% of the global output. The key growth area has been in the production of added value zirconium oxides (zirconias) and zirconium chemicals.
China now accounts for more than 60% of the production of zirconium oxides (zirconia) and zirconium chemicals and the consumption of zircon sand for this application has grown to around 120,000mts a year.
The global capacity for zircon sand now stands at around 1.25 million tonnes a year with Australia remaining the largest producer at around 450,000mts a year and South Africa second on 430,000mts. The USA is the third largest producer at around 200,000mts and Indonesia has increased its output in the last few years to a level of 100,000mts.
Iluka Resources of Australia is the largest producer of zircon sand with 9 mines in Australia and 2 mines in the USA. Iluka tends to set the benchmark in global pricing for zircon sand and at the start of 2008 the price was at USD 800-850/mt CIF China and ended the year at USD 850-900/mt CIF China.
China is the largest importer of zircon sand at a level of around 500,000mts in 2008 and this has been growing at an annual rate of 10% a year for the last 3 years. The import value for China in 2008 was around USD 400 million.
China has a small output of zircon sand relative to its consumption. The annual output is around 20,000mts. The use of Chinese zircon sand has been limited by he higher radioactivity levels which makes it unsuitable for many applications.
The global supply and demand of zircon sand was thought to be fairly balanced in 2008 at 1.25m tonnes. The level of growth has been stable at around 4% a year in the last 5 years but with the global economic slow-down it is thought demand will remain flat or decline slightly to 1.20m tonnes in 2009.
New zircon sand mines are scheduled to come on stream over the next 2 years in Australia, Mozambique, Madagascar, Gambia, Russia, South Africa, India and Canada. These mines could introduce a further 150-200,000mts of zircon sand per year.
With some decline in demand and increased output, the price of zircon sand is likely to remain in the region of USD 800-900/mt during 2009.
In the last 6 months the price of premium grade zircon sand, the feedstock for most zirconium chemicals and oxides, has increased sharply. In July 2010 the price was USD 900/mt and this has now risen to USD 1200/mt and is expected to reach USD 1400/mt in Q1 2011.
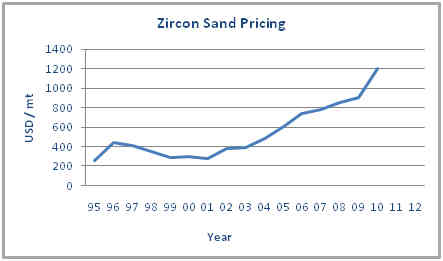
The effect of both an increase in consumer demand and a reduction in supply has led to tightness in the market. All the main producers, including Iluka Resources, Rio Tinto and Exxaro, have shown declining output due partly to ageing mines. At the current time only Iluka Resources shows signs of increased output through its new Australia operations, Murray and Eucla Basins.
In the next two years the expected annual production output for zircon sand will be 1.4 million mts against a demand of 1.6 million mts.
This expected shortfall will continue to put an upward pressure on zircon sand prices throughout 2011 and 2012 which in turn will lead to upward pressures on the pricing of zirconium chemicals and oxides.